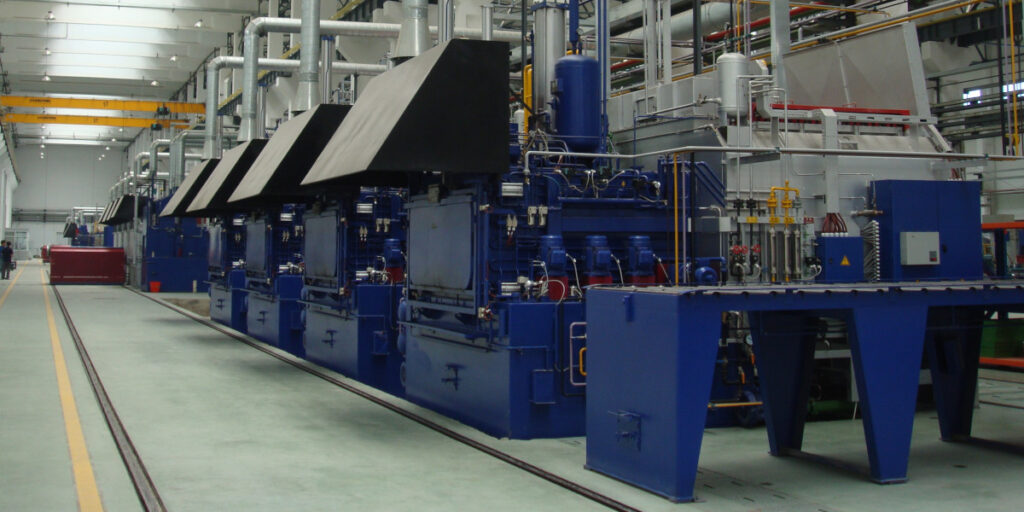
- Atmosphere Batch Type Furnace in TQ configuration. Meaning the work pieces are loaded directly inside the hotzone from one side and then automatically transported to the quench chamber after heat treatment process and unloaded from the other side. This configuration gives highest throughput at the cost of a slightly larger foot print. RTQ configuration is also available to allow the loading and unloading from one direction to reduce space requirements.
NESDRA’s atmosphere furnaces available as batch or continuous types are real work horses to get you reliable, repeatable, consistent and low cost heat treatment result.
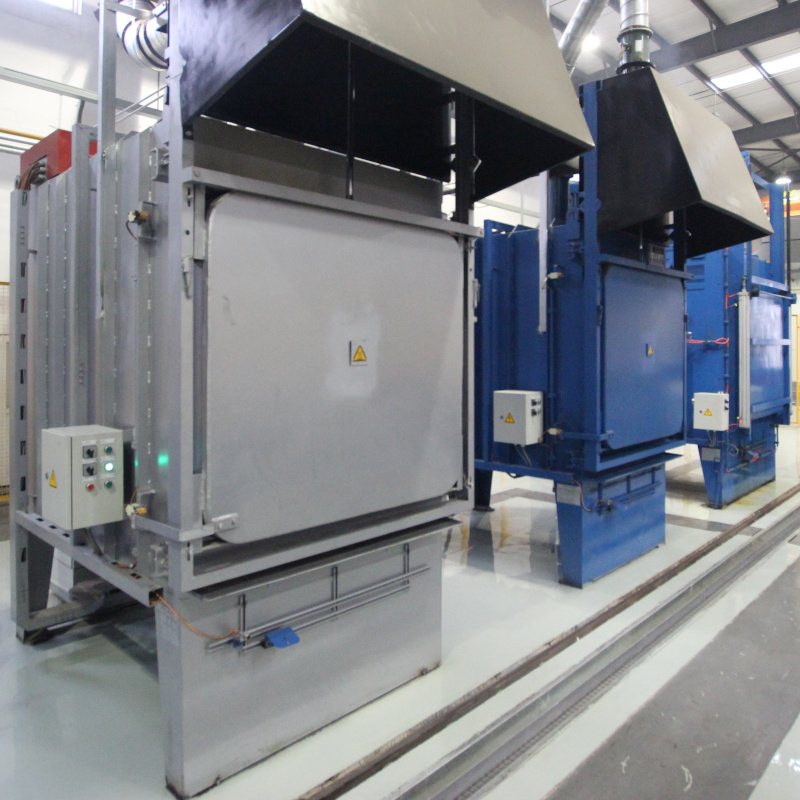
Atmosphere furnace standard temperature uniformity is ±5 °C and feature superior insulation to avoid unnecessary heating losses, thus significantly reduce operating cost.
Atmosphere furnaces (Process Temperature < 1050 °C) are most commonly used for hardening with oil quench and carburizing and case hardening, though other more specialized heat treatment processes are also supported.
Tempering furnaces (Process Temperature < 750 °C) are most commonly used for tempering, annealing, nitriding, pre-heating and stress relieving, but special solutions like water quench are also available.
NESDRA’s atmosphere continuous furnaces deliver large production rates that reduce processing costs per piece.
Equipment is engineered and customized to customers required heat treatment process, throughput needs and available layout.
NESDRA delivers a reliable heat treatment solution capable of achieving
the desired metallurgical results at the best value possible.

2. High quality long lasting bricking with a vaulted ceiling as a standard to ensure a uniform radiation of the charges from all directions, in combination with atmosphere circulation and heating system results in a temperature uniformity of ±5 °C.
Very robust design of all critical components to ensure long service life with low operating and maintenance cost, resulting in high equipment availability. German engineering standards and stringent quality control at all production steps.
3. Attention to detail in all aspects of the manufacturing process, results in great fit and finish, therefore reliable operation and easy maintenance for years to come.
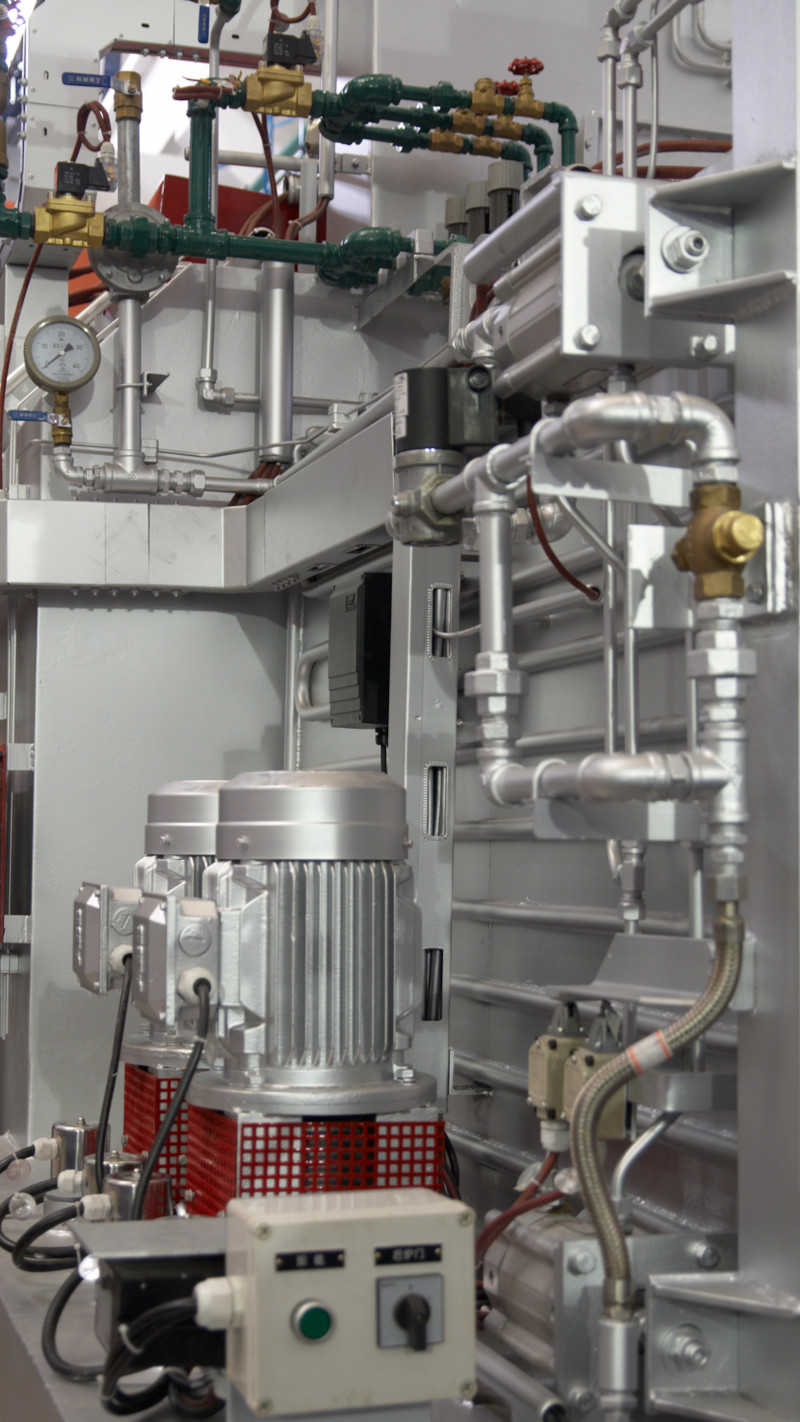