Графитовая горячая зона — король, но металлическая горячая зона — королева
За последние несколько десятилетий в отрасли термообработки произошли значительные изменения в типе материала горячей зоны, который чаще всего используется в вакуумных печах. В 1970-х годах почти 90 % установленных горячих зон были полностью металлическими. Однако сегодня около 80 % изготовляются из графита.
За последние несколько десятилетий графитовая изоляция значительно улучшилась в отношении термической стабильности и надежности изделия в широком диапазоне температур и областей применения. Поэтому сейчас она значительно экономичнее, более устойчива к ошибкам в эксплуатации и экономит энергию, чем полностью металлическая горячая зона.
Если соблюдать достаточную осторожность, графитовая горячая зона даст приемлемые результаты для большинства применений вакуумной обработки.
Тем не менее, полностью металлическая горячая зона сохранила свое применение в таких чувствительных процессах, как диффузионное склеивание и пайка алюминия.
Преимущества использования полностью металлических горячих зон включают в себя лучшую степень утечки, более высокие максимальные уровни вакуума, улучшенные возможности откачки вакуума, более чистую рабочую среду, более быстрое охлаждение с помощью газа и меньшую вероятность загрязнения деталей.
К недостаткам полностью металлических горячих зон относятся, прежде всего, более высокая стоимость приобретения и эксплуатации.
Основы теплоизоляции и отопления
Чтобы понять разницу между материалами горячих зон и, следовательно, оптимальный вариант использования полностью металлических и полностью графитовых горячих зон, нам необходимо сделать шаг назад и понять принципы теплопередачи.
Существует три способа передачи тепла: излучение, кондукция и конвекция. Чтобы выполнять свою работу, вакуумная горячая зона должна справляться со всеми из них.
Проще говоря, излучение отвечает за нагрев поверхности заготовки, а кондукция — за проникновение тепла от поверхности заготовки к ее центру. Конвекция может играть или не играть роль в вакуумной печи.
- Внутри вакуумной печи основным способом передачи тепла является излучение или радиационное тепло. Без него заготовка не сможет нагреться. Радиационное тепло — это избыточная энергия атома, которая выделяется в виде электромагнитной волны. Электромагнитная волна будет излучаться нагревателем внутри горячей зоны и двигаться до тех пор, пока не будет поглощена чем-то на своем пути. Надеемся, что это будет заготовка, которую нужно нагреть. Именно такой способ доставки тепла использует наше солнце. Радиантное тепло не требует среды или промежуточного материала для передачи тепла. На самом деле вакуум — это оптимальное условие для передачи радиационного тепла, поскольку в вакууме нет газа, способного рассеивать или поглощать его. В связи с этим, хотя радиационное тепло необходимо для нагрева заготовок, в то же время изоляционная система вакуумной печи должна быть специально разработана для снижения поглощения радиационного тепла.
- Когда заготовка поглощает радиационное тепло на поверхности, происходит кондуктивная или теплопроводная передача тепла к сердцевине заготовки за счет прямого столкновения молекул. В микроскопических масштабах кинетическая энергия молекул изменяется прямо пропорционально их температуре. Так, при повышении температуры молекулы увеличивают свое движение и приобретают кинетическую энергию. Затем они сталкиваются с более холодными молекулами, передавая им свою кинетическую энергию и, следовательно, тепло. Это означает, что для работы теплопроводности необходим прямой контакт горячих и холодных частей. Поэтому горячая зона, спроектированная таким образом, чтобы минимизировать пути передачи теплопроводности изнутри горячей зоны наружу, будет иметь большой эффект изоляции с точки зрения предотвращения выхода тепла из горячей зоны посредством кондукции.
- Последний способ передачи тепла — конвекция, которая возникает, когда «быстрые» молекулы газа движутся в пространстве и ударяются об другие молекулы. Вспомните «пар», выходящий при кипячении воды. Горячая зона должна быть спроектирована с учетом конвективной теплопередачи, хотя, пока камера находится под вакуумом во время работы, этот способ теплопередачи практически не существует, поскольку конвекция требует присутствия молекул газа для передачи тепловой энергии, а в вакуумированной камере молекул мало.
Для работы конвекционного нагрева горячая зона должна быть заполнена газом (обычно азотом или аргоном) и вентилятором для циркуляции тепла ко всем деталям в загрузке ( изделиям). В отличие от радиационного нагрева, детали не обязательно должны находиться в зоне прямой видимости нагревательных элементов, чтобы получить тепловой эффект, что обеспечивает более равномерный нагрев.
Таким образом, конвекционный нагрев играет в вакуумной печи роль в улучшении скорости нагрева и равномерности температуры ниже 850 °C, поскольку радиантный метод передачи тепла менее эффективен при более низких температурах.
Еще один случай, когда конвекционный нагрев играет важную роль, — это использование парциального давления (здесь также происходит дозаправка газа в горячую зону во время работы), например, для предотвращения испарения элементов, присутствующих в изделиях (таких как хром в нержавеющих сталях). Конвекция также играет важную роль при газовой закалке под высоким давлением.
Таким образом, хорошо спроектированная горячая зона будет иметь сопла-заслонки, которые впускают газ, используемый для конвекционного нагрева, и задерживают его внутри горячей зоны, одновременно циркулируя вокруг загрузки (заготовок), чтобы достичь более «скрытых» областей заготовок. Это сделает нагрев гораздо более энергоэффективным и предотвратит потери тепла, не позволяя горячему газу покидать горячую зону. В то же время во время закалки сопла заслонок открываются, чтобы закалочный газ циркулировал в горячей зоне и удалялся из нее, проходя через теплообменник для охлаждения.
Поскольку аспекты теплопередачи внутри вакуумной горячей зоны теперь понятны, давайте рассмотрим аспекты изоляции.
Существует несколько вариантов изоляции, характерных для вакуумных печей:
- полностью металлическая конструкция горячей зоны
- полностью графитовая конструкция горячей зоны
- Композитные конструкции, использующие как металлическую, так и графитовую или керамическую изоляцию
Полностью металлическая конструкция горячей зоны
Полностью металлические горячие зоны построены из металлических щитов, состоящих из молибдена и нержавеющей стали с воздушными зазорами (или, возможно, более точно, вакуумными зазорами) между ними для замедления передачи лучистой энергии.
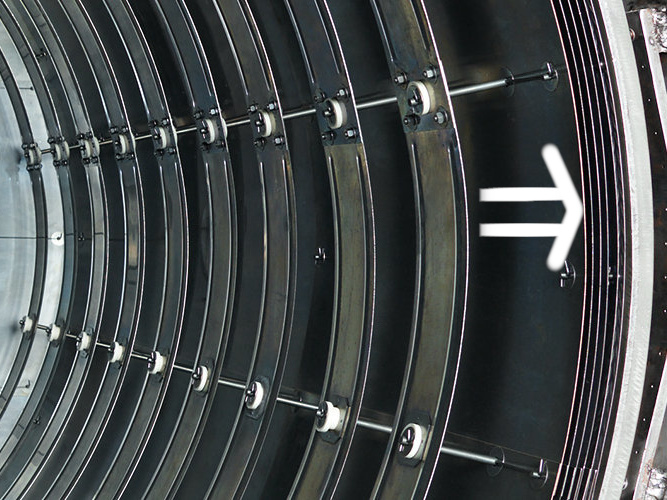
Количество тепловых щитов и материалы их изготовления зависят от температурного режима печи (см. рис. 1). Каждый экран обладает дополнительным изолирующим эффектом. Обычно система включает в себя пять или шесть щитов, два или более слоев молибдена на горячей стороне, а затем несколько слоев нержавеющей стали типа 304 или 316.
Молибден обладает превосходной (в пять раз меньшей) излучательной способностью и гораздо более высокой термостойкостью, чем нержавеющая сталь. Эта пониженная излучательная способность позволяет ему отражать больше лучистого тепла и поглощать меньше. Поэтому главное, чтобы теплозащитный экран отражал лучистое тепло обратно в детали и передавал лишь небольшое количество лучистого тепла следующему слою щита. Поэтому двух слоев молибдена обычно достаточно для значительного снижения температуры, поэтому в следующих слоях горячей зоны, которые приближаются к водоохлаждаемой стенке вакуумного сосуда, можно использовать щиты из нержавеющей стали.
Недостатком молибдена является то, что охрупченные («рекристаллизованные») тепловые щиты легко разрушаются по границам зерен при ударной нагрузке и подвержены повреждениям в промышленных условиях, поэтому при осмотре или обслуживании полностью металлической горячей зоны необходимо соблюдать особую осторожность.
Важность излучательной способности
Полностью металлическая изоляционная система в значительной степени зависит от ее способности отражать лучистое тепло. Излучательная способность определяет долю лучистой энергии, которую материал, например металлический рефлектор, поглощает, по сравнению с тем, сколько он отражает. Поэтому следует выбирать материал с низкой излучательной способностью и поддерживать ее на протяжении долгого времени.
Однако способность материала отражать излучение зависит от самого материала, длины волны излучаемого тепла, которая сама по себе диктуется его температурой и степенью окисления.
Температура внутри вакуумной горячей зоны является вспомогательным фактором, поскольку она помогает еще больше снизить излучательную способность, однако именно окисление необходимо контролировать в процессе эксплуатации.
Загрязнение полностью металлической изоляционной системы
Молибден имеет показатель излучательной способности 0,13 при 950 °C и немного лучше при более высокой температуре (это означает, что он поглощает только 13% тепла излучения и отражает остальное), в то время как полированная сталь типа 316 имеет показатель 0,66, а окисленная сталь будет близка к показателю излучательной способности 0,9.
Поэтому основной проблемой полностью металлических изоляционных систем является потеря излучательной способности из-за загрязнения металлических теплозащитных щитов. Это может произойти из-за утечки воздуха в камеру, кислорода / водяного пара, присутствующего в линиях подачи инертного газа, или загрязненного инертного газа. Магистрали заполнения, регуляторы, клапаны и другие компоненты подвергаются значительным эксплуатационным нагрузкам во время повторяющихся циклов закалки и повторного нагрева.
Хотя новое оборудование является герметичным, после нескольких лет эксплуатации уплотнения и резьбовые соединения начинают протекать, компоненты выходят из строя, а мягкие паяные соединения могут растрескиваться. Это позволяет воздуху проникать в камеру и вызывать поверхностное окисление и потускнение тепловых экранов и внутренней части печи.
В результате проникновения воздуха снижается отражающая способность щитов, а поскольку они изолируют, отражая лучистое тепло, этот процесс потускнения резко снижает эффективность изоляции полностью металлической изоляционной системы.
Один из способов обнаружить это (помимо визуального) — следить за потреблением электроэнергии, которое будет расти по мере ухудшения тепловой эффективности горячей зоны. В какой-то момент печь, которая, возможно, изначально требовала всего 50-60 % установленной мощности, с трудом достигает температуры даже при 90-100 % потребляемой мощности.
Помимо постепенного загрязнения, вызванного утечками воздуха, теплозащитное покрытие может быть окислено в случае непредвиденных обстоятельств, таких как открытие двери печи при повышенной температуре или выход из строя какого-либо компонента, позволяющего проникнуть воздуху. Насыщенный кислородом воздух быстро проникает внутрь и загрязняет теплозащитные щиты. Это может быть настолько серьезным, что печь становится непригодной для использования, несмотря на попытки запустить циклы водородной очистки, что приводит к необходимости замены защитных экранов.
Еще один способ изменения излучательной способности теплозащитных экранов — выделение загрязняющих веществ из загрузки (заготовок), таких как масла, смазки, клеящие вещества, паяльные пасты и другие продукты выделения газов, которые со временем накапливаются и делают щиты неэффективными. Чтобы предотвратить это, необходимо позаботиться о надлежащей очистке заготовок перед тем, как они попадут в вакуумную печь.
Еще одним источником загрязнения теплозащитного покрытия является влага с завода во время загрузки и разгрузки печи или если печь выключена и оставлена открытой, когда она не работает. Если точка росы воздуха ниже температуры холодной стенки, происходит конденсация влаги, которая под действием вакуума выделяет кислород и вызывает окисление теплозащитного покрытия.
Полностью графитовая конструкция горячей зоны
Популярной альтернативой горячим зонам с металлической изоляцией является изоляция на основе графита. Типичная конструкция для максимальной рабочей температуры 1400 ºC состоит из графитового материала толщиной 50 мм, обычно в виде (войлочного) одеяла или плиты. Нередко используется два или более слоев материала.
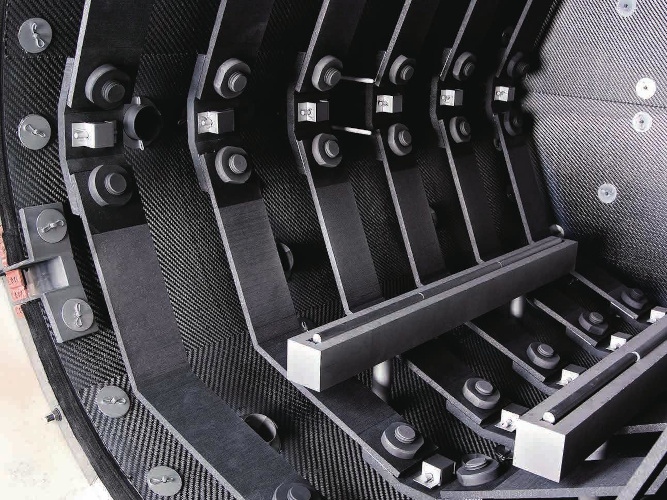
К тому же внешняя камера печи обычно охлаждается водой, а большинство процессов происходит в вакууме или в атмосфере частичного давления, что еще больше снижает теплопередачу.
Графитовое одеяло или плита обычно укладываются слоями, причем при монтаже слои укладываются в шахматном порядке, чтобы свести к минимуму вероятность образования непрерывных промежутков между внутренними и внешними слоями и последующих потерь тепла.
Изделия из одеял впоследствии могут быть покрыты графитовой краской, а изделия из графитовых плит могут поставляться с покрытием лицевой стороны графитовой фольгой или углеродным композитом, соединенным с фольгой (CFC). Это улучшает отражение (т. е. снижает излучательную способность) тепла от графитовых нагревателей обратно к заготовкам, а также защищает поверхность от повреждения технологическими или закалочными газами.
Между слоями графитовых плит также могут быть промежуточные слои фольги. Эти дополнительные слои фольги обеспечивают повышенную эффективность изоляции.
В системе графитовой изоляции графитовое одеяло/плита обладает низкой теплопроводностью, что препятствует передаче тепла от горячей стороны к холодной.
Обладая теплопроводностью в три раза лучше (ниже), чем у металлической теплозащиты, эти системы обеспечивают превосходные изоляционные характеристики по сравнению с полностью металлическими горячими зонами и, как правило, стоят дешевле и требуют меньше времени на установку.
Различные слои графитовой изоляции препятствуют излучению тепла изнутри горячей зоны, что сводит к минимуму теплопередачу к оболочке, поддерживающей изоляцию, и, в конечном счете, к холодной стене.
Благодаря низкой проводимости графита такие горячие зоны обычно более энергоэффективны, чем полностью металлические конструкции.
Одним из недостатков графитовых материалов является их высокая удельная теплоемкость (cp) — свойство, определяющее, сколько тепловой энергии может удержать материал. По сравнению с молибденом, распространенным металлическим теплозащитным материалом, удельная теплоемкость графита более чем в два раза выше. Таким образом, при данном весе графита сохраняется в два раза больше тепловой энергии, чем при использовании молибдена.
Это приводит к несколько сниженной способности к закаливанию, поскольку для снижения температуры изоляции требуется часть охлаждающей мощности закалочного газа.
Помимо того, что тепловая масса изоляции содержит избыточное тепло, графит также (по своей конструкции) является плохим проводником, поэтому его тепло задерживается внутри графитовых волокон, задерживая отдачу его тепловой энергии при закалке.
С другой стороны, несколько разделенных слоев теплозащиты, используемых в конструкции полностью металлической изоляции, позволяют закалочному газу свободно проходить между ними, обеспечивая более быстрое охлаждение.
Газовая эрозия
Рассматривая графитовую изоляцию, следует помнить о возможности эрозии материала из-за износа закалочным газом. Эта проблема чаще всего наблюдается в диапазоне давлений 6 — 20 бар на открытых стыках и проходах через плиты при быстрой газовой закалке. По этой причине многие из этих мест закрываются или покрываются другим материалом, например молибденом или углеродным композитом. При давлении 20 бар закалочный газ, такой как азот, имеет массу 51 кг/м3, поэтому легко понять, как высокоскоростная газовая закалка может так легко разрушить графитовую плату.
Помимо снижения эффективности изоляции из-за потери толщины изоляции, другой проблемой, возникающей в результате газовой эрозии, является образовавшийся мелкий графитовый порошок. Этот порошок переносится закалочным газом через теплообменник и воздуходувку системы газовой закалки. Затем он скапливается внутри ребер теплообменника, снижая его эффективность. Кроме того, графитовый порошок может загрязнить работу и помешать процессу, выполняемому в печи.
Удаление связующего
Помимо эрозии от закалочного газа, еще одним источником образования летучего графитового порошка является испарение связующего из плиты (так называемое удаление связующего). Без связующего графит высвобождается в виде мелкого порошка, который может загрязнить процесс и засорить систему охлаждения закалочного газа, как это может сделать абразивный порошок.
Разложение графита при воздействии кислорода
Основной проблемой при использовании графитовой изоляции является возможность ее разложения под воздействием воздуха. При наличии кислорода при температуре выше 300°C углерод, входящий в состав графита, соединяется с кислородом, образуя CO и CO2.
(1) C + ½O2 = CO и C + O2 = CO2
В результате графит медленно превращается в газ CO и CO2, который удаляется из печи с помощью насосной системы. Сначала появятся небольшие ямки, которые часто выглядят как «сахарный кубик», а по мере дальнейшего разложения графит продолжает терять массу и просто исчезает.
Выводы
Большинство современных вакуумных печей для термообработки оснащаются графитовыми горячими зонами, учитывая огромную универсальность этого материала.
За последние несколько десятилетий графитовая изоляция значительно улучшилась в отношении термической стабильности и качества продукции в широком диапазоне температур и областей применения.
Как и во всех вакуумных печах с металлической изоляцией, герметичная система вакуумной печи гарантирует, что воздух (кислород) и водяной пар не попадут в горячую зону.
Чистые и сухие детали, поступающие в печь, продлевают общий срок службы всех материалов горячей зоны.
В результате графитовая горячая зона подходит для большинства требований к термообработке, но все же следует выбирать металлическую горячую зону, если:
- Процесс не терпит случайного попадания пыли или грязи. К таким чувствительным процессам относятся диффузионное соединение и пайка алюминия.
- Технологический цикл требует высоких температур и скорости нагрева более 30 °C в минуту.
- Технологический цикл требует очень высокой равномерности температуры в диапазоне около +/- 3 °C.
Также следует учитывать, как материалы могут реагировать с углеродом в графитовой печи. Графитовая пыль снижает температуру плавления и может оказывать неблагоприятное воздействие на некоторые материалы — вплоть до эвтектических реакций.
В вышеперечисленных случаях для обеспечения оптимальных результатов лучше всего использовать полностью металлическую горячую зону.