Начало и эволюция вакуумного газового закаливания
До внедрения газовой закалки под высоким давлением в вакуумных печах можно было удовлетворительно закаливать только некоторые виды горячедеформированных сталей и несколько других инструментальных сталей небольшого сечения.
Затем, в 1975 году, компания ИПСЕН представила первую однокамерную вакуумную печь с газовой закалкой. В этой печи использовался мощный двухскоростной турбинный вентилятор, обеспечивающий давление закалки 0,5 МПа, а также теплообменник и направляющая потока для оптимизации скорости потока и турбулентности для оптимальной равномерности закалки.
Для вакуумной термической обработки в вакуумную печь было внесено множество изменений в общую систему охлаждения, и в настоящее время практически все холодно- и горячекатаные стали, а также быстрорежущие стали могут успешно подвергаться вакуумной закалке с использованием газовой закалки под высоким давлением до 2 МПа или 20 бар.
Для вакуумной термообработки низколегированных сталей, требующих еще более высокой производительности закалки, предлагаются многокамерные вакуумные печи, которые могут быть сконфигурированы с отдельными камерами для закалки газом высокого давления или маслом. Это, конечно, дороже в приобретении и эксплуатации, а при использовании масляной закалки требуется дополнительное оборудование, например, моечные машины для очистки деталей, выходящих из масляной ванны.
Почему вакуумная газовая закалка так популярна?
Термообработка в соляных ваннах и атмосферных печах все чаще заменяется обработкой в вакуумных печах с закалкой газом под высоким давлением по целому ряду причин:
- Вакуумная термообработка гарантирует идеальную защиту поверхности, исключая риск обезуглероживания и окисления. Практически исключается шероховатость и искажение поверхности, что позволяет снизить затраты на окончательную обработку, которые могут быть весьма значительными, особенно если учесть, что заготовка после термообработки обычно твердая на поверхности и поэтому очень трудно поддается обработке.
- Дегазация поверхностей и идеальные условия вакуума обеспечивают лучшую прочность при одинаковых уровнях твердости и более длительный срок службы.
- Надежный сбор данных о процессе и воспроизводимость, благодаря автоматической термообработке и точному контролю всех критических факторов, обеспечивают стабильный и повторяемый результат.
- Специальные возможности включают комбинированную пайку и закалку за одну операцию, а также безопасный отжиг без обезуглероживания использованных инструментов для повторной обработки.
- Идеальные условия работы без неприятной жары, без загрязнения окружающей среды и без возникновения проблем со сливом отходов.
- Запрограммированная автоматическая обработка, мгновенная готовность установки к работе и гибкость в управлении приводят к значительной экономии рабочих затрат.
В результате вакуумная газовая закалка или переход к вакуумной масляной закалке позволяет добиться еще более высоких результатов.
Доступные методы охлаждения в вакуумной печи
После завершения термообработки в вакуумной печи существует три способа охлаждения заготовки:
- Вакуумное охлаждение — считается самым медленным методом охлаждения, при котором тепло отводится из печи, а тем временем вакуумные клапаны остаются открытыми. Затем печь охлаждается без добавления газа или использования рециркуляционного вентилятора. Этот метод также зависит от способности горячей зоны к удельным потерям тепла при охлаждении. Для достижения температуры окружающей среды с 1350°C потребуется около 14 часов.
- Статическое охлаждение — при использовании этого метода вакуумные клапаны закрываются, и печь заполняется инертным газом до установленного давления, но не более расчетных возможностей печи. Клапан подачи инертного газа открывается и закрывается для поддержания требуемого уровня давления в печи во время цикла охлаждения. При таком способе охлаждения не используется рециркуляционный вентилятор, но повышенное присутствие инертного газа сводит на нет изоляционные характеристики горячей зоны, что значительно увеличивает скорость охлаждения за счет конвективных теплопотерь. Для достижения температуры окружающей среды с 1350°C потребуется примерно половина времени вакуумного охлаждения.
- Принудительное охлаждение — начинается с закрытия вакуумных клапанов и заполнения печи инертным газом до заданного уровня (отрицательного или положительного). Как только давление в печи достигает -16 кПа (и продолжает расти, пока не будет достигнуто определенное заданное значение), включается рециркуляционный вентилятор для охлаждения загрузки («заготовки») и печи путем перемещения горячего газа через теплообменник с водяным охлаждением. Как и при статическом охлаждении, клапан подачи газа открывается и закрывается для поддержания необходимого уровня давления в печи во время цикла охлаждения. Это самый быстрый метод, который позволяет охладить печь с 1350°C до температуры окружающей среды примерно за 2 часа.
Как увеличить скорость отвода тепла
Увеличить массовый расход газа (скорость)
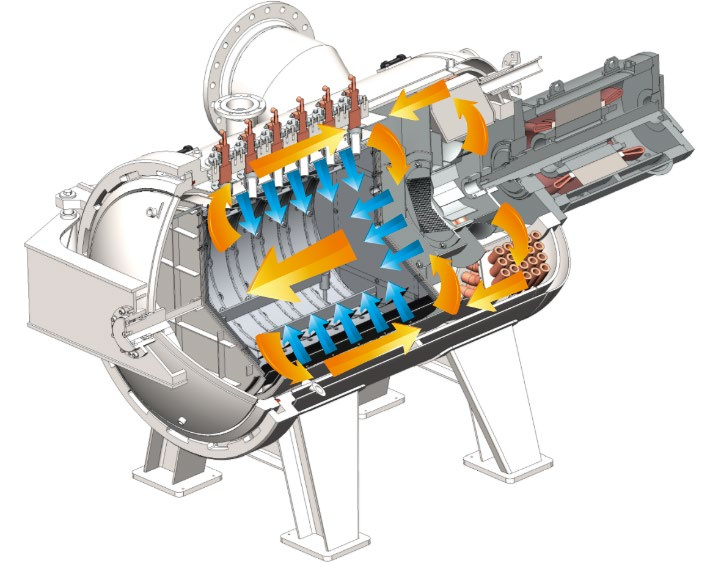
Когда компания ИПСЕН в 1970-х годах внедрила закалку под высоким давлением в вакуумной печи, было осознано значительное влияние давления на отвод тепла. Чем выше давление газа, тем больше тепла отводится. Сложность заключается в том, что в одной камере, которая используется для нагрева и закалки, давление газа можно увеличить только настолько, чтобы не повредить горячую зону. Поэтому, если давление газа необходимо увеличить еще больше, операцию закалки нужно перенести в отдельную камеру, предназначенную только для закалки газом высокого давления или маслом. Так появилась многокамерная вакуумная печь.
Влияние мощности воздуходувки на скорость охлаждения
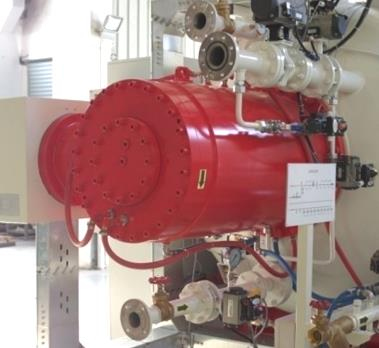
Закалочный вентилятор состоит из турбинного колеса с приводом от электродвигателя, герметично закрытого в вакуумном корпусе. Производительность воздуходувки зависит от размера колеса, скорости его вращения и возможности изменения скорости во время цикла закалки.
Поэтому в настоящее время газовые закалочные печи премиум-класса оснащаются частотными преобразователями, двигателями с регулируемой скоростью вращения и возможностью запуска вентилятора под вакуумом для сокращения времени подготовки к закалке.
Влияние эффективности теплообменника на скорость охлаждения
В высокопроизводительных газовых закалочных печах премиум-класса используются медные трубчатые ребра с водяным охлаждением. Она стоит дороже, но по теплопередаче превосходит сталь или алюминий.
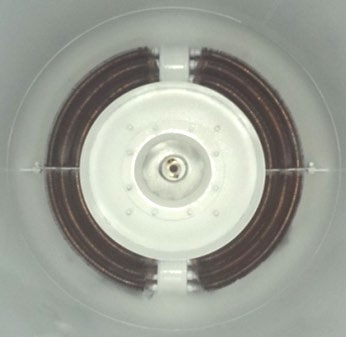
Влияние состава закалочного газа на скорость охлаждения
Оптимальный закалочный газ будет иметь низкую плотность, чтобы минимизировать количество энергии, необходимое для его продувания через закалочный контур. Он также будет обладать высокой удельной теплотой, которую можно рассматривать как меру его способности отводить тепло от загрузки (обрабатываемых деталей). Кроме того, он не должен вступать в реакцию с материалами, которые он охлаждает.
Исходя из доступности, плотности и удельных тепловых свойств, водород представляется хорошим выбором в качестве закалочного вещества. Однако из-за взрывоопасности, связанной с водородом, он редко используется в качестве закалочного газа в промышленной термообработке. Азот является наиболее популярным выбором, прежде всего потому, что он легко доступен и недорог. При давлении около 20 бар он оказывает такое же закалочное действие, как и масло. Аргон используется в некоторых специальных случаях, но он закаливает не так эффективно, как азот, и стоит значительно дороже. Гелий также обладает отличными свойствами в качестве закалочного газа; он используется довольно часто, особенно для материалов, которые имеют ограничения по закаливаемости при газовой закалке.
Влияние конструкции вакуумной камеры и распределения загрузки (заготовок) на скорость охлаждения
Хорошо известен факт, подтвержденный полевыми испытаниями и компьютерным моделированием, что характер потока закалочного газа через загружаемые детали и вакуумную камеру может оказывать значительное влияние на скорость охлаждения загружаемых деталей. Этот эффект существует независимо от давления закалки, размера воздуходувки или любых других факторов, которые уже обсуждались. Учтите, что скорость газа значительно снижается уже через 50 см после выхода из сопла. Таким образом, расположение сопла и направление закалки газа могут существенно повлиять на то, сможет ли ваша однокамерная вакуумная печь достичь необходимых характеристик закалки газа или нет.
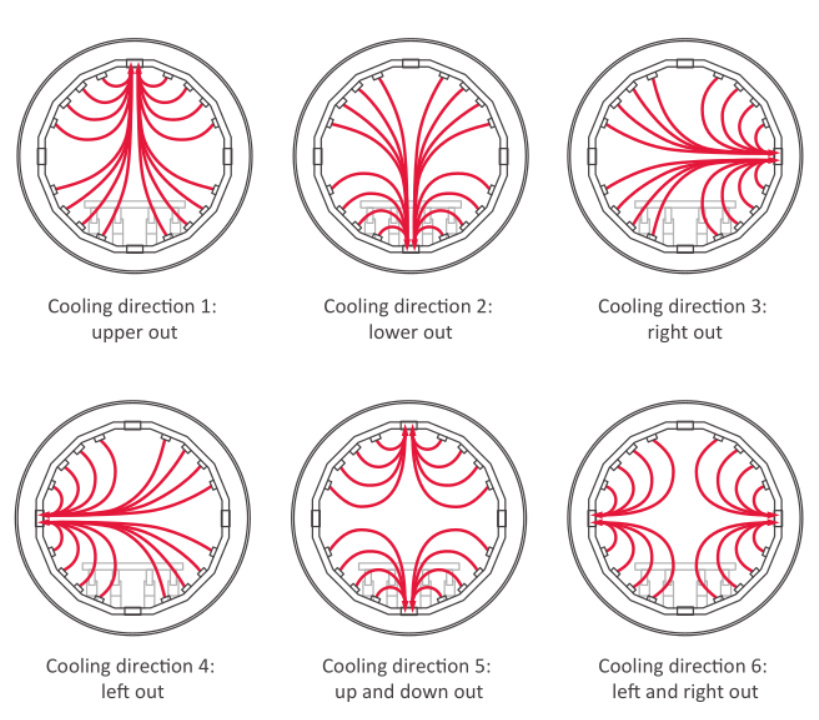
Контрольные показатели скорости вакуумной газовой закалки
Испытание на охлаждение нашей вакуумной газовой закалочной печи премиум-класса при давлении газа (N2) 15 бар с образцом материала H13 500 кг (400 x 400 x 400 мм):
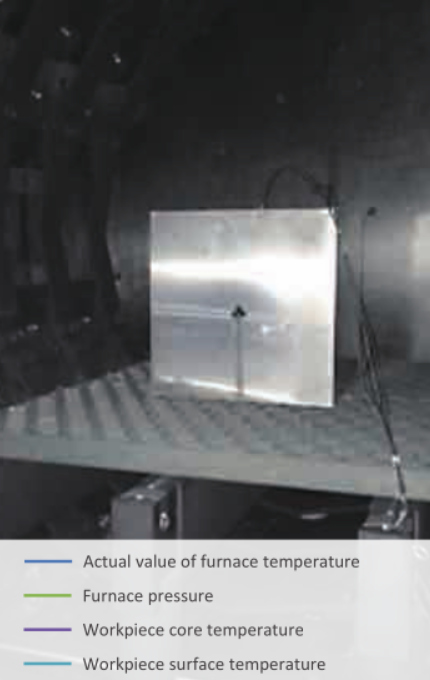
Диапазон охлаждения: 1020 °C — 540 °C
Скорость охлаждения на поверхности: 96 °C/мин
Скорость охлаждения в сердцевине: 11,4 °C/мин
Диапазон охлаждения: 400 °C — 250 °C
Скорость охлаждения на поверхности: 18,8 °C/мин
Скорость охлаждения в сердцевине: 5,5 °C/мин
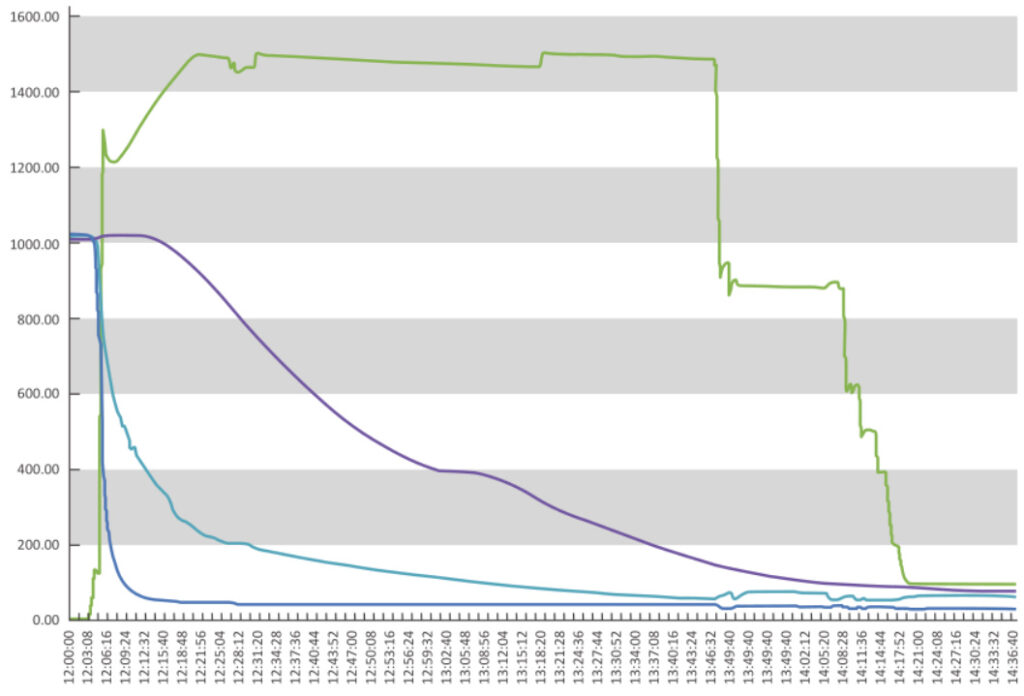
Испытание на изотермическое закаливание. Охлаждение до 400 °C, затем выдержка, чтобы позволить температуре сердцевины догнать температуру поверхности. Современные системы управления позволяют полностью контролировать цикл закалки.
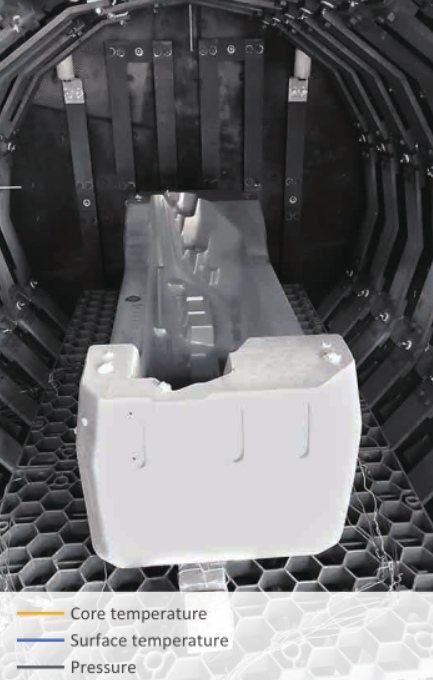
Изотермическая начальная температура: 400 °C
Конечное изотермическое состояние: разность температур ядра и поверхности 100 °C
Температура поверхности колеблется < 20 °C
Время окончания изотермического процесса: 17 минут
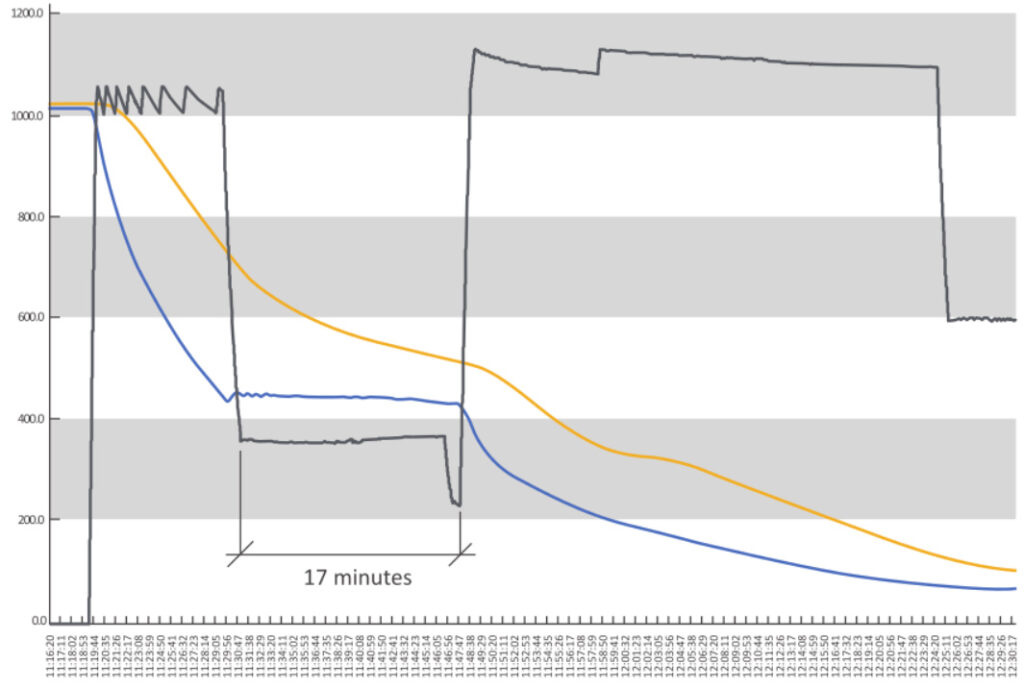