Обзор вакуумной печи для азотирования
Наш популярный образец вакуумной печи для азотирования представляет собой предварительно откачанную ретортную печь, которая является отличным решением для широкого спектра процессов и применений.
Она имеет горизонтальную кубическую зону нагрева и может нагреваться конвекцией с использованием защитного газа. Она оснащена передовой системой управления печью, которая позволяет осуществлять автоматический контроль и, следовательно, стабильную, экономичную и качественно контролируемую термообработку азотированием, а также точный контроль слоя азотирования на заготовках.
Реторта / горячая зона может работать в условиях низкого вакуума при температуре до 850 °C.
Оборудование также может использоваться для нитроцементации, предварительного окисления, последующего окисления, отпуска и других видов термообработки.
Система включает в себя следующие компоненты:
- Горячая зона
- Реторта
- Вакуумная система
- Модуль азотирования и нитроуглероживания (опция)
- Система прямой циркуляции газа и охлаждения (опция)
- Система косвенного охлаждения (реторта и изоляция)
- Панель смешивания технологических газов
- Шкаф электропитания и управления процессом
Вакуумная ретортная печь для азотирования работает с высокой равномерностью температуры и гарантирует высокое качество, точность и повторяемость процессов термообработки.
Конструктивное исполнение печи вакуумного азотирования
Горячая зона
Кубовидная горячая зона состоит из окрашенного корпуса из углеродистой стали, который поддерживает теплоизоляцию из керамического волокна. Железно-хромо-алюминиевые ленточные нагревательные элементы установлены по обеим сторонам горячей зоны, равномерно распределенные по внутренней поверхности изоляции.
Во время охлаждения отверстия внизу и вверху обеспечивают циркуляцию воздуха через нагревательные элементы и между изоляцией и ретортой.
Корпус печи сварен на четырех опорных стойках, поэтому его можно поставить на пол завода.
Между опорами расположены рельсы для загрузочной тележки.
Реторта
Реторта является горизонтальной, с круглым сечением, и изготовлена из нержавеющей стали AISI 304.
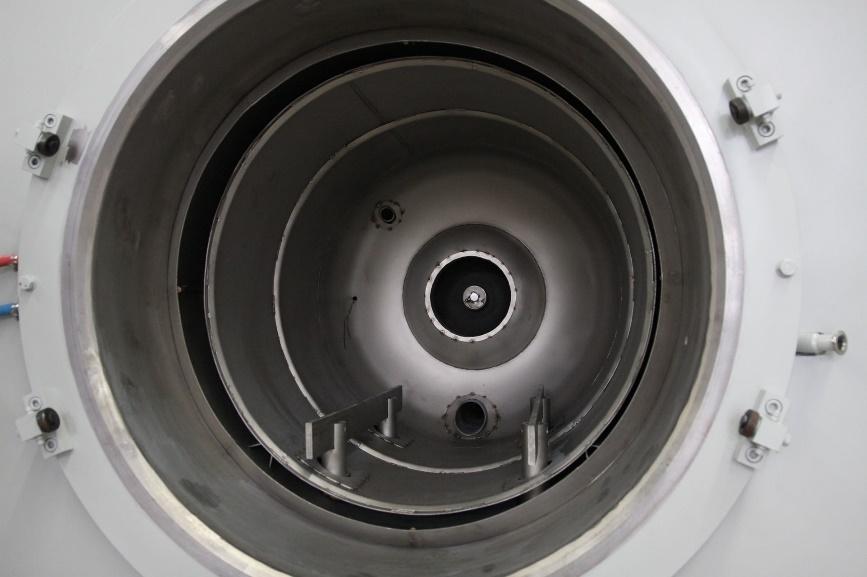
Передняя дверь изолирована и снабжена водоохлаждаемым губчатым уплотнением.
Дверь открывается справа налево, так как она закреплена на держателе, который соединяет ее с шарниром, установленным на корпусе горячей зоны.
Для фиксации двери на корпусе реторты используется механизм байонетного закрытия. Дверь запирается с помощью электропривода.
Внутри реторты два жестких стержня из AISI 304, опирающиеся на штифты, равномерно распределенные по длине рабочей зоны, обеспечивают плоскую опору для загрузки (заготовок).
Система вакуумирования
Вакуумная насосная система разработана в соответствии с критериями низкого вакуума и состоит из следующих компонентов и функций:
Пластинчато-роторный насос (ы) — Leybold SV 200
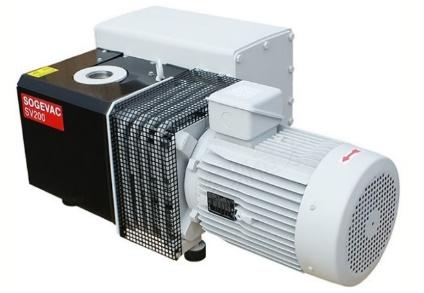
Клапаны приводятся в действие пневматически, а их движение контролируется ограничительными выключателями.
Установлены предохранительные клапаны повышенного давления.
На вакуумном трубопроводе имеется отверстие для обнаружения утечек для удобства обслуживания и обнаружения утечек.
Вакуумный манометр — вакуумная камера оснащена манометром Пирани. Уровни вакуума отображаются в цифровом виде на человеко-машинном интерфейсе (HMI).
Пластинчато-роторный насос изолирован от трубопроводной системы гибкими соединениями сильфонного типа. Эти соединения минимизируют вибрации, передаваемые в печную камеру.
Защита от превышения давления установлена между печью и вакуумным насосам. Вакуумная система оснащена блокировками для обеспечения безопасных условий эксплуатации. Блокировки системы управления сконструированы таким образом, чтобы обеспечить «отказоустойчивость» в случае отключения электроэнергии.
Модуль азотирования и нитроуглероживания
Система подачи технологического газа включает в себя следующие компоненты:
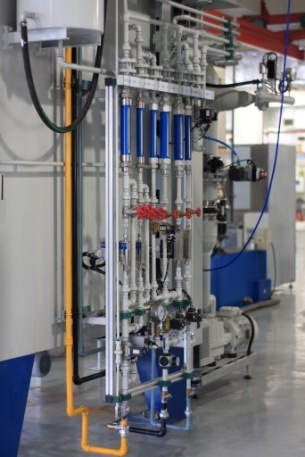
- Один диссоциатор аммиака
- Один водородный зонд
- Одна горелка
- Один быстродействующий пневматический электромагнитный клапан для безопасной промывки реторты азотом
- Расходомеры, клапаны, реле давления, манометры и трубопроводы
В диссоциаторе — крекинге аммиака — аммиак разделяется на два составляющих компонента: азот и водород. Аммиак проходит через нагретую трубу, содержащую катализатор, и полученная смесь газов поступает в реторту.
Специальный зонд непрерывно измеряет содержание водорода в реторте и подает соответствующий выходной сигнал в систему управления, которая рассчитывает азотный потенциал kn, регулирует поток аммиака через диссоциатор и перекалибрует наиболее подходящую смесь технологических газов для запрограммированного процесса азотирования.
Технологический газ выходит из реторты в помещение после прохождения через фильтр и диссоциатор в систему сжигания, установленную в задней части печи.
В случае тревоги реторта быстро промывается азотом, чтобы печь оставалась в безопасных условиях.
Система прямой циркуляции газа и охлаждения
Опциональная система циркуляции газа гарантирует эффективную передачу тепла от реторты к загрузки (заготовкам) и равномерное распределение температуры по всему рабочему объему.
Система включает в себя вентилятор и распределительный цилиндр, оба из AISI 304.
Двигатель вентилятора имеет водяное охлаждение, вакуумную герметичность и примыкает непосредственно к корпусу, поэтому динамическое уплотнение вала, соединяющего двигатель с вентилятором, не требуется.
Распределительный цилиндр обеспечивает равномерную циркуляцию технологического газа внутри горячей зоны и через загрузку («изделия»), что повышает теплопередачу и гарантирует высокую равномерность температуры.
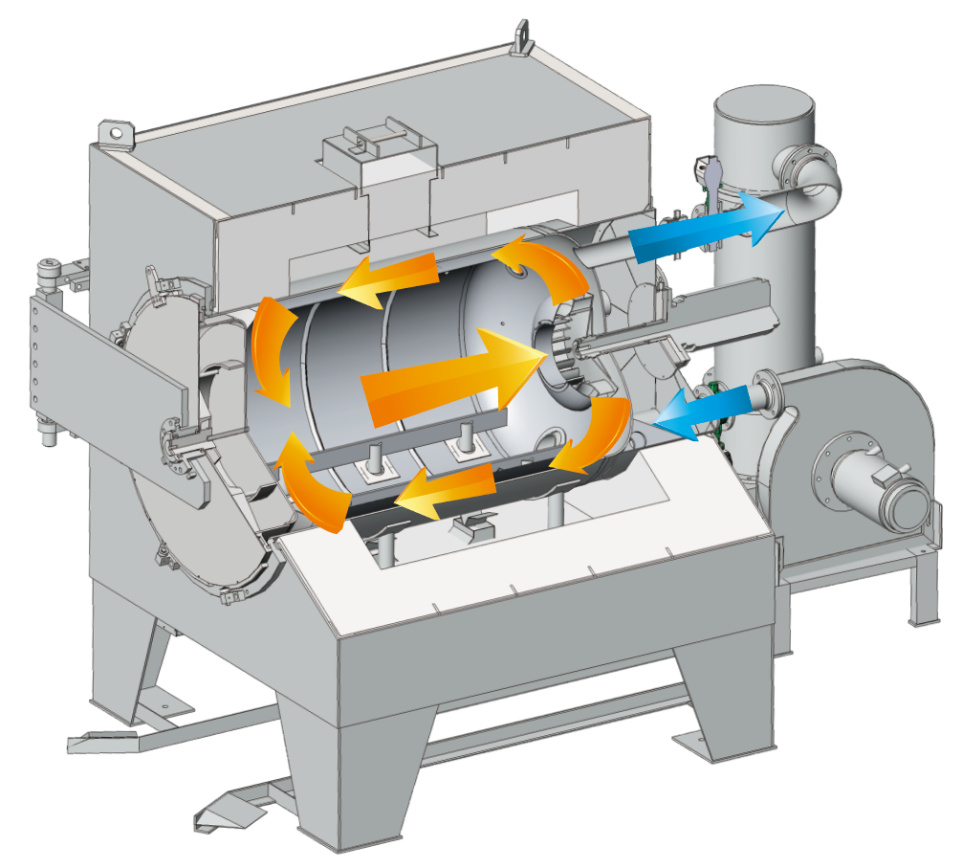
В качестве опции предлагается система прямого газового охлаждения. Она включает в себя высокопроизводительную воздуходувку, теплообменник и вакуумплотную оболочку.
На этапе охлаждения горячий технологический газ внутри реторты циркулирует из реторты через теплообменник, где он передает тепло воде, циркулирующей во вторичном контуре.
Охлажденный технологический газ затем возвращается в реторту, где отводит остаточное тепло от загрузки (заготовок), что повышает скорость охлаждения и сокращает время цикла.
Система косвенного охлаждения
В нижней части корпуса печи установлена воздуходувка. Холодный воздух из окружающей среды проникает через зазор между внутренней изоляционной стенкой печи и ретортой и выводится в верхней части печи. Воздух выпускается в цех.
Эта система обеспечивает быстрое охлаждение как реторты, так и теплоизоляции из керамического волокна.
Шкаф для электропитания и управления технологическими процессами
Силовые и контрольные приборы размещены в отдельно стоящем шкафу распределения питания и управления процессом.
Внутри электрического шкафа установлены пускатели двигателей и автоматические выключатели для электродвигателей. Для других электрических линий установлены автоматические выключатели. Для обслуживания предусмотрены блокировочные разъединители на лицевой стороне шкафа или стратегически расположенные блокировочные местные разъединители, чтобы минимизировать время простоя и обеспечить безопасность.
Шкаф распределения питания и управления процессом имеет одно электрическое подключение и обеспечивает питание компонентов печи. Кабель может быть подведен к шкафу сверху или снизу, в зависимости от требований заказчика.
В шкафу размещаются следующие приборы и компоненты:
- ПЛК Siemens
- Промышленный ПК с 19-дюймовым человеко-машинным интерфейсом
- Температурный контроллер Eurotherm
- Прибор защиты от перегрева Eurotherm
- Главный выключатель
- Измеритель мощности
- Аналоговые амперметры для измерения тока в нагревательных элементах.
- ИБП — источник бесперебойного питания
- Андоновая лампа (зеленая, желтая и красная)
- Акустическое сигнальное устройство
- Набор внутренних лампочек безопасности
- Вентилятор для впуска свежего воздуха
Две термопары типа К обеспечивают подачу измерительных сигналов на приборы контроля температуры. Одна термопара устанавливается снаружи реторты и используется для контроля мощности, подаваемой на нагревательные элементы, другая термопара устанавливается внутри реторты и используется для контроля температуры, записи и предотвращения перегрева.
Мощность нагрева, подаваемая на нагревательные элементы, регулируется с помощью тиристора.
Вакуумметр подает измерительный сигнал на ПЛК. Уровень вакуума отображается на человеко-машинном интерфейсе.
Средства защиты и предохранения
Печь спроектирована и изготовлена в соответствии с действующими нормами охраны труда и техники безопасности. Система управления печью имеет блокировки безопасности, которые защищают операторов оборудования от травм и предотвращают повреждение печного оборудования во время нормальной работы печи.
Блокировки и предохранительные устройства включают, в частности, следующее:
- В случае выхода из строя контрольной термопары ПЛК останавливает нагрев и подает сигнал тревоги.
- В случае перегрева в горячей зоне прибор перегрева останавливает нагрев, и система подает сигнал тревоги.
- В случае отсутствия электроэнергии вакуумный клапан отключается до безопасного положения.
- В случае отсутствия потока охлаждающей воды в распределительной системе ПЛК останавливает нагрев печи и подает сигнал тревоги.
Дверь печи можно открыть только тогда, когда давление внутри вакуумной камеры сравняется с атмосферным.
Витрина: Результаты азотирования
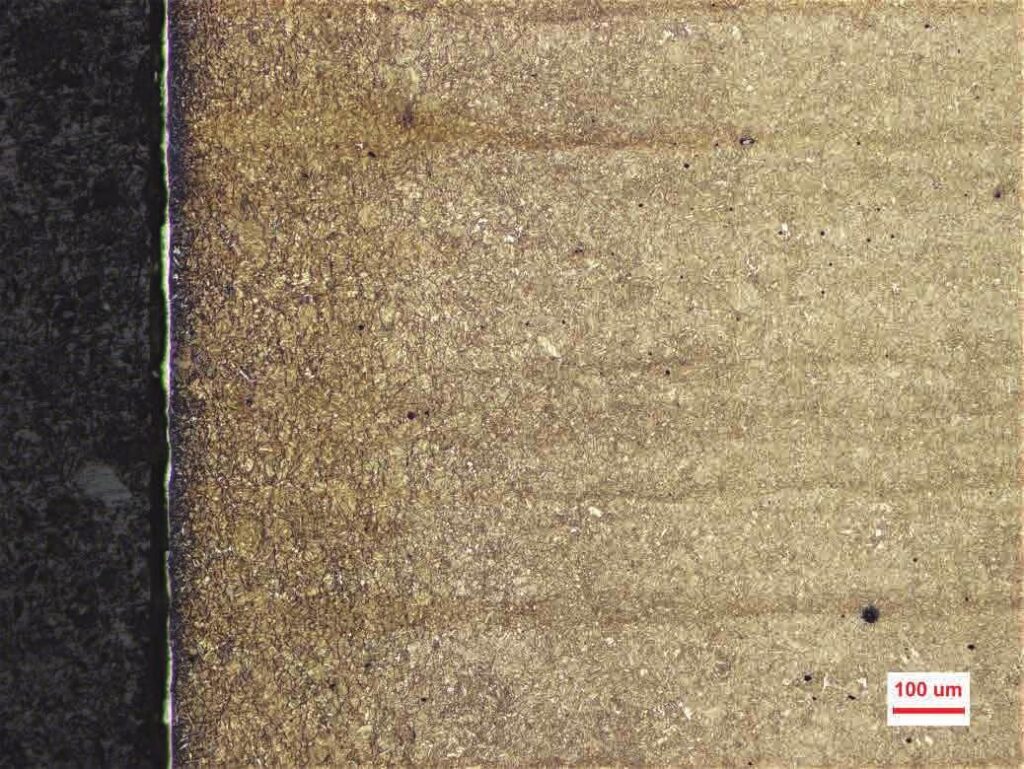
Азотирование 35CrMoV
Глубина азотированного слоя 0,75 мм
Поверхностная твердость 640HV1
Твердость сердцевины 333HV1
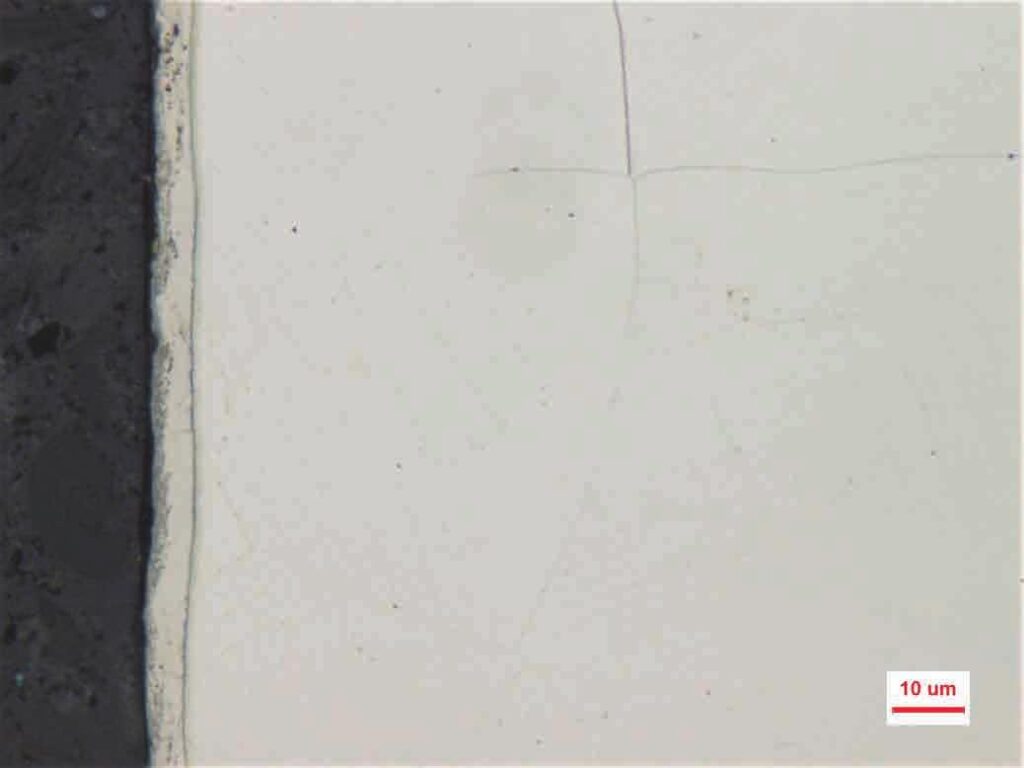
Азотирование 304
Глубина азотирования ~ 5.2μm
Поверхностная твердость 710HV0.05
Твердость сердцевины 250HV0.3
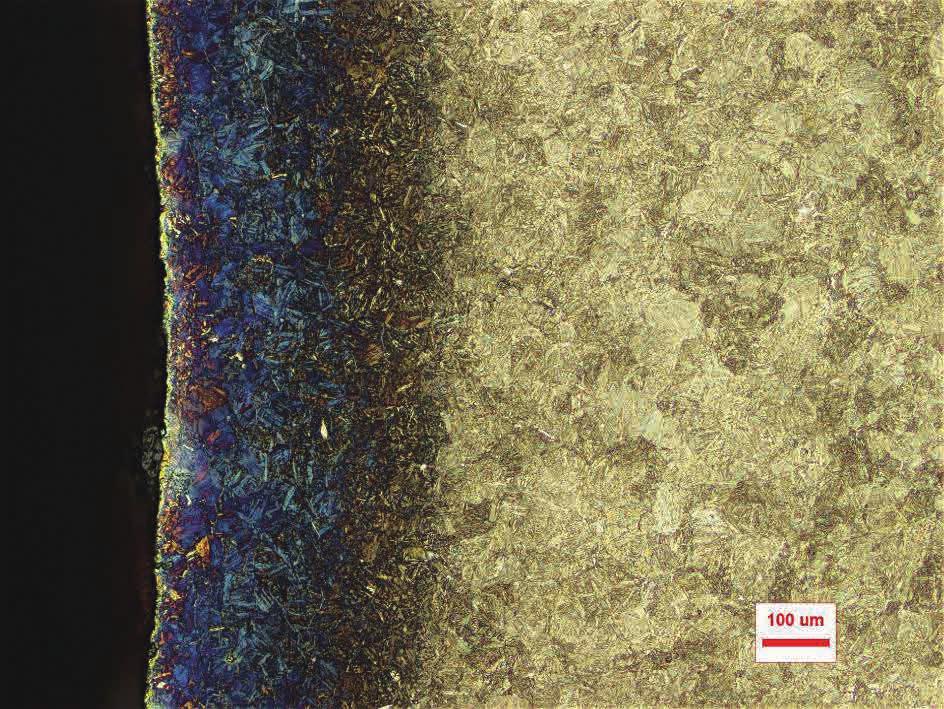
Азотирование материала 38CrMoAl
Нет слоя соединения
Поверхностная твердость ~ 970HV1
Глубина азотирования 0,42 мм
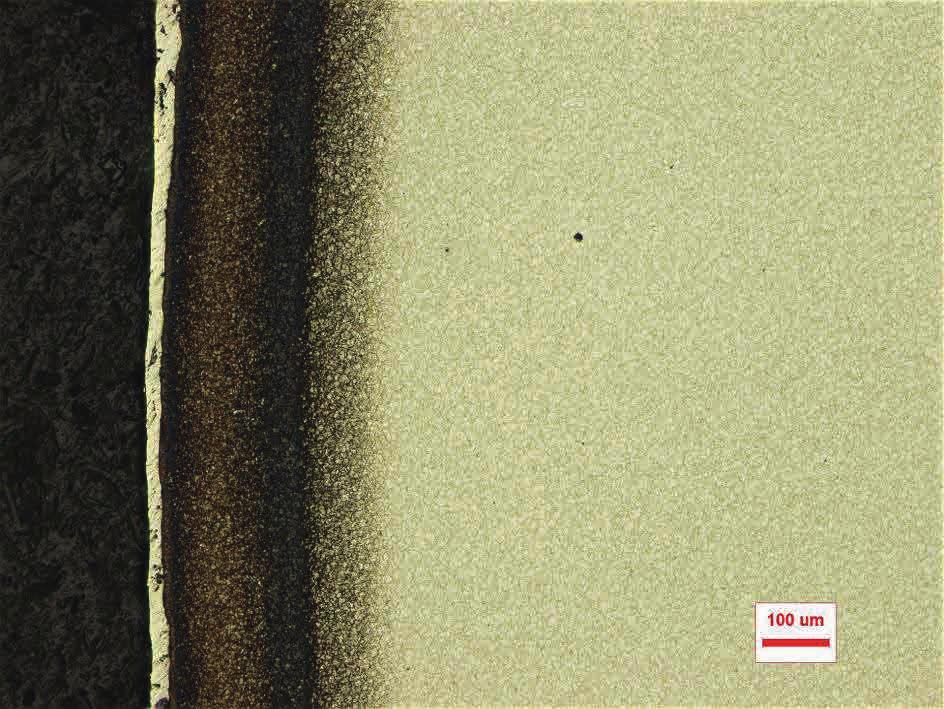
Азотирование H13
Белый слой, показанный на картинке, — это алюминиевая фольга. Нет слоя соединения
Поверхностная твердость ~ 940HV1
Глубина азотирования 0,32 мм
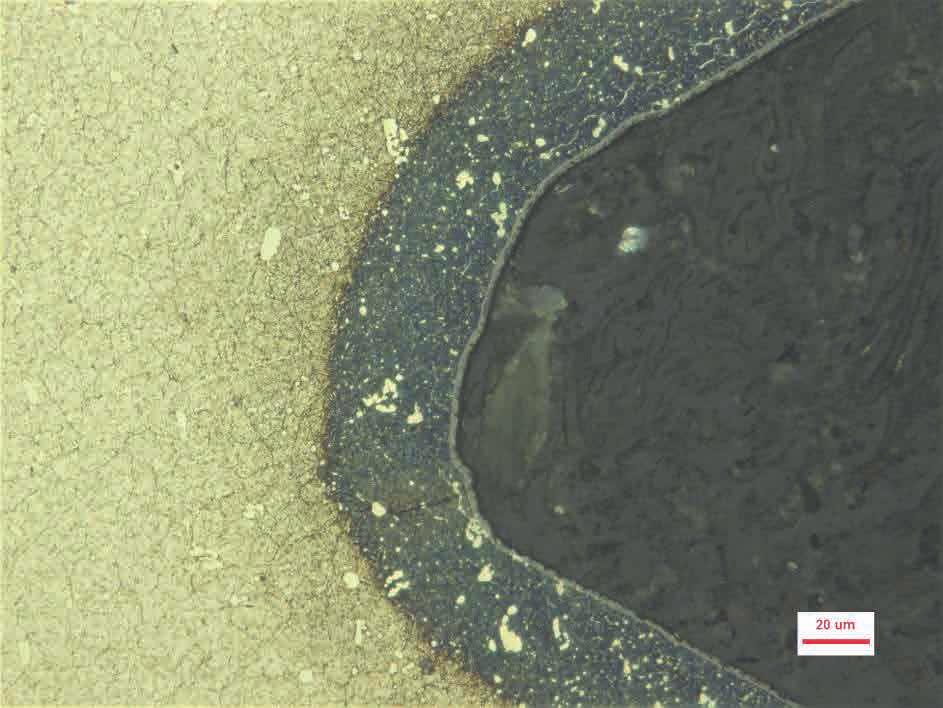
DC53 Азотирование
Пост-оксидный слой 1,8 мкм
Твердость сердцевины 760HV0.3
Поверхностная твердость ~ 1072HV0.1
Глубина азотирования 0,12 мм
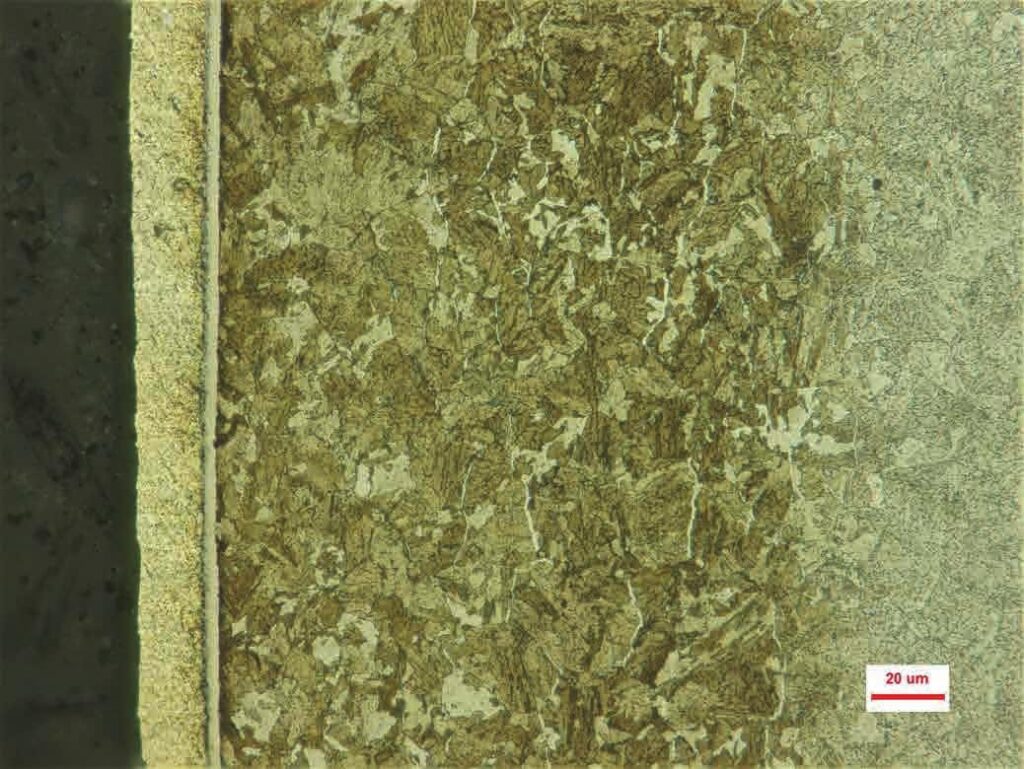
Нитридирование 25Cr3Mo
Глубина слоя компаунда 2,9 мкм
Твердость сердцевины 237HV0.3
Поверхностная твердость ~ 842HV0.1
Глубина азотирования 0,30 мм