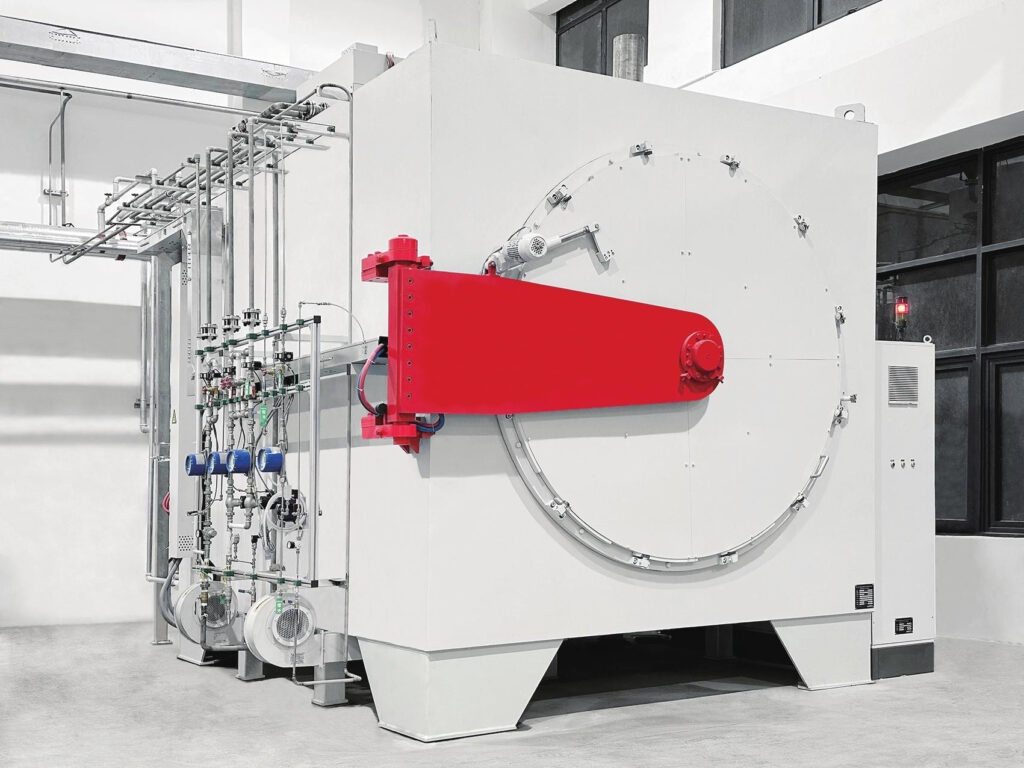
- Nitriding furnace with vacuum sealed heat resistant steel retort. Furnace can be pre-evacuated and heated up with protective gas. It can achieve stable, economical and efficient precisely controlled nitriding, nitrocarburizing, post oxidation, tempering, annealing and other heat treatment.
NESDRA’s vacuum furnaces are engineered for precise control at molecular level to achieve repeatable and challenging heat treatment process requirements.
The furnaces are used for annealing, brazing, carburizing, hardening, sintering, surface treatments and tempering.
Specialized processes like vacuum carburizing with acetyline, low pressure carburizing, solution nitriding, etc … are of course also available as an option.
Premium graphite and metal hot zones for exceptional temperature uniformity of up to ±3 °C, fast heating, energy efficiency due to quality insulation and long service life.
Convection heating is always included to achieve better uniformity in heating work-pieces and decrease cycle time.
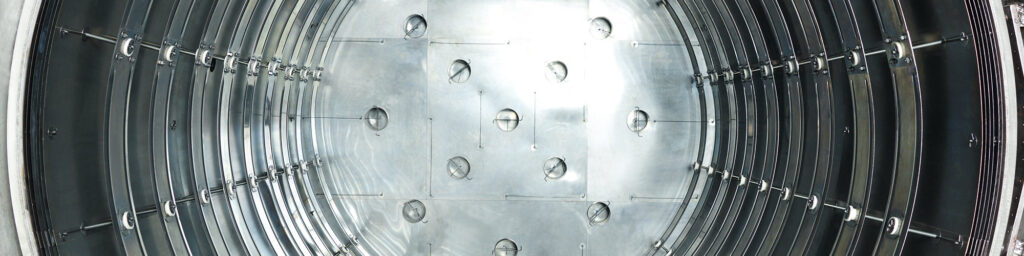
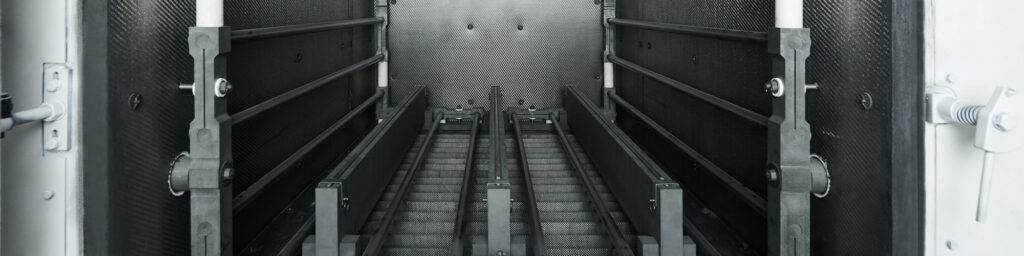
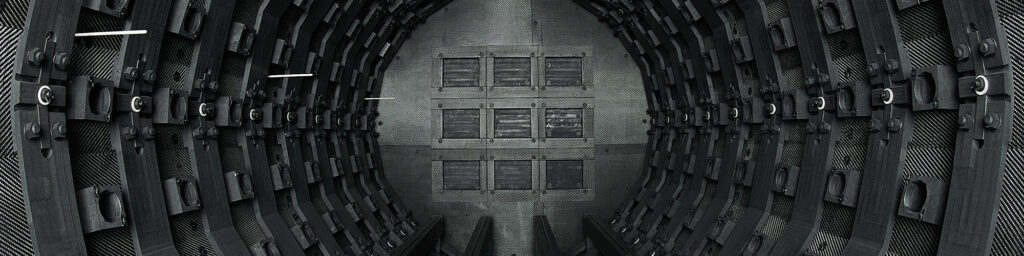
Fully automated vacuum heat treatment modular line that includes a number of independent vacuum heating chambers and gas, oil and salt quenching chambers to provide high production capacity and maximum flexibility for a wide range of applications in the automotive and in the aviation industries.
The independent heating & quenching modules in the line can carry out different thermal and thermochemical treatment processes at the same time, or can remain switched off, depending on the production capacity requirements.
The load shuttle module is a vacuum chamber provided with heating system that transfers the load from the parking/loading
positions to the hot zone modules, then to the quenching chambers, and finally back to the parking/unloading stations.
Only the best is good enough for our vacuum furnaces.
We use best in class components and materials.
Vacuum systems from Pfeiffer, Agilent and Leybold. Graphite is sourced from Kureha, SGL and Tokai. We use Festo for pneumatic systems and electrical control cabinet is based on ABB and Siemens components.
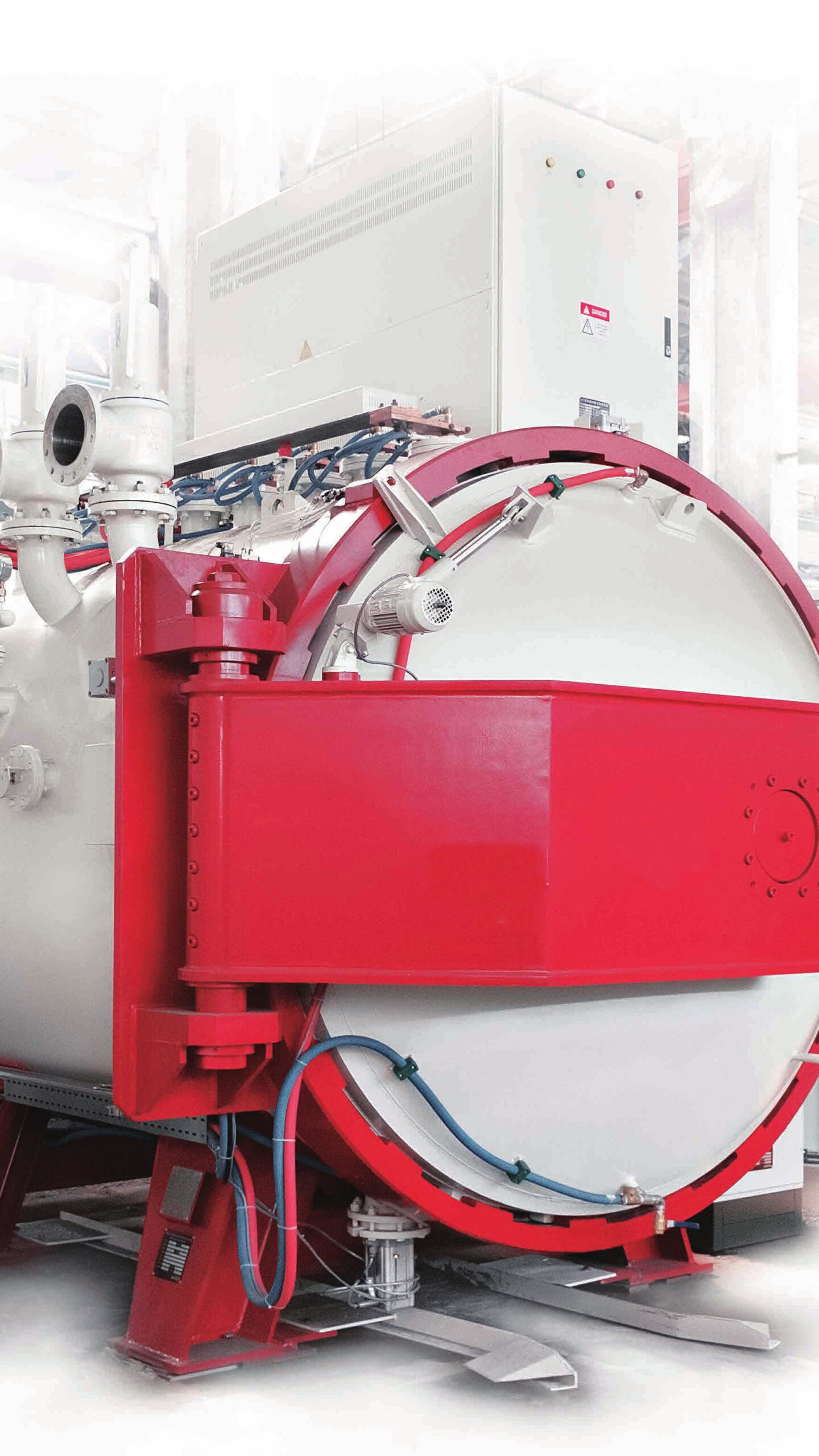
2. Single chamber vacuum heat treatment furnace. Maximum quenching pressure is up to 20 bar. Quench gas flow directions choice from 360 degrees to unidirectional.
We offer wide range of quenching options to meet even the most challenging cooling speed requirements of the tool and die industry.
3. Multi chamber vacuum heat treatment furnace with modular option to have gas, oil, salt and water quenching. A three chamber design with a transfer chamber in the middle can realize rapid transfer from heating to quenching of the work-pieces without pollution of the heating chamber with the quench medium.
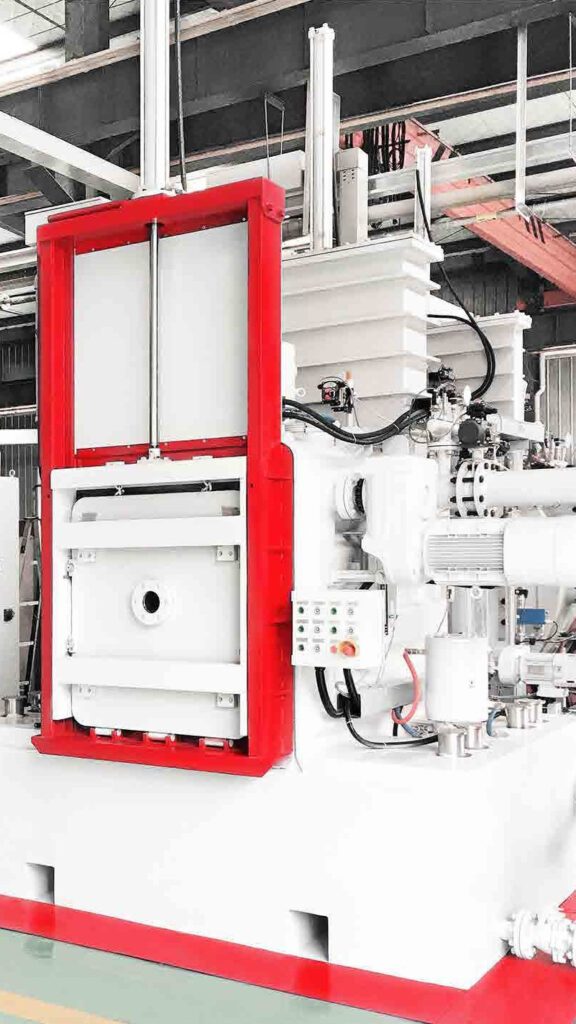